Wednesday 18th December 2024
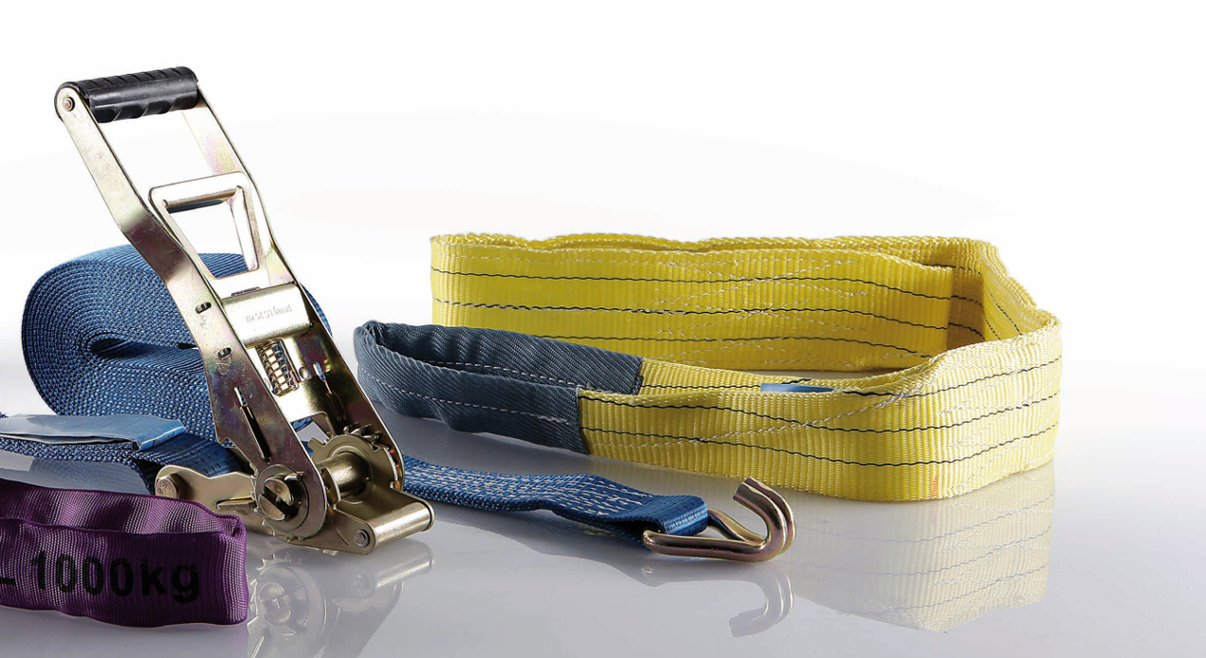
- Introduction to Textile Slings: An overview of what they are and their importance.
- Advantages of Textile Slings: The main benefits that set them apart.
- Common Materials Used: A summary of the materials involved in their production.
- Types of Textile Slings: In-depth information on webbing, round, flat, and endless slings
- Applications of Textile Slings: The industries and situations where they works great.
- Safety Standards and Regulations: Guidelines and certifications for safe practices.
- Inspection and Maintenance: Suggestions for prolonging the life of textile slings.
- Factors to Consider When Choosing a Textile Sling: Practical tips for selecting the appropriate sling.
- Comparison with Other Sling Types: The advantages and disadvantages of textile slings compared to alternatives like chain and wire rope slings.
- Conclusion and Best Practices: A summary with actionable advice for effective usage.
Introduction to Textile Slings
What distinguishes textile slings is their ability to adapt to the shape of the load, which helps minimize the risk of damage to delicate surfaces while ensuring excellent grip and control. Their lightweight design makes them easy to handle, transport, and store, reducing strain on workers and enhancing overall efficiency. Additionally, textile slings are resistant to corrosion, UV exposure, and certain chemicals, making them suitable for use in various environments.
These characteristics have made textile slings essential across industries such as construction, manufacturing, shipping, and logistics. Whether lifting prefabricated materials at construction sites or safely moving sensitive equipment in factories, textile slings help ensure that tasks are completed safely and efficiently. Their adaptability and user-friendly nature make them a preferred choice for professionals who prioritize safety and performance in their lifting operations.
Advantages of Textile Slings
1. Lightweight and Easy to Handle
The soft and flexible design of textile slings ensures minimal risk of damage to fragile or sensitive loads, such as glass, polished metals, or painted surfaces. Their ability to conform to a load's shape provides better support and reduces pressure points.
3. High Strength-to-Weight Ratio
Despite being lightweight, textile slings are incredibly strong and capable of handling heavy loads. Manufactured from durable synthetic materials like polyester or nylon, they offer impressive load capacities while maintaining flexibility.
Textile slings are resistant to rust, corrosion, and degradation from exposure to UV rays, moisture, and chemicals. This makes them an excellent choice for outdoor and industrial environments where harsh conditions are a concern.
Available in various configurations such as webbing, round, and endless slings, textile slings can be tailored to suit a wide range of lifting needs. They are suitable for handling irregularly shaped or oversized loads with ease.
Textile slings are often more affordable than chain or wire rope alternatives, making them a cost-effective choice for businesses. Their durability and low maintenance requirements further enhance their value.
Textile slings operate quietly, unlike their metal counterparts. Their soft material minimizes the risk of injuries from sharp edges or accidental bumps, enhancing safety in the workplace.
8. Compact Storage and Transportation
Textile slings can be easily rolled or folded, taking up very little storage space. Their lightweight and compact design also makes them easy to transport between different job sites.
Textile slings are produced in accordance with international safety standards like EN 1492, ensuring they perform reliably in various conditions and maintain a high safety factor during lifting tasks.
Many textile slings are crafted from recyclable or eco-friendly materials, offering a sustainable alternative to conventional lifting solutions.
Common Materials Used
Textile slings are made from high-strength synthetic materials, each chosen for its unique properties to meet different lifting needs. Knowing about these materials can assist in selecting the right sling for a specific application:
Polyester is the most widely used material for textile slings because of its excellent strength-to-weight ratio and resistance to stretching. It works well in environments where moisture, mild chemicals, or UV exposure is a concern, as it retains its integrity under these conditions. However, polyester is not the best choice for environments with strong alkalis.
Nylon is known for its high elasticity, making it an excellent option for absorbing shock loads. It is resistant to abrasion and performs well in environments that involve alkalis. However, it is not suitable for acidic environments, as acids can degrade its fibers over time.
Polypropylene is lightweight and cost-effective, often used for less demanding applications. It has good resistance to moisture and certain chemicals but is not as durable under heavy loads or extreme conditions compared to polyester and nylon.
Types of Textile Slings
1. Webbing Slings
Advantages: They are lightweight, flexible, and easy to manage. The flat design offers a broad load-bearing surface, which helps to minimize pressure on the item being lifted.
Applications: Perfect for lifting pallets, machinery, or fragile items like glass or painted surfaces.
Advantages: They boast exceptional strength with a high strength-to-weight ratio. The round shape ensures even load distribution, which helps to alleviate stress points.
Applications: Ideal for lifting heavy or oddly shaped loads, such as pipes, equipment, or containers.
3. Endless Slings
A continuous loop of webbing or synthetic fibres that provides complete versatility in usage.
Advantages: They can be utilized in various configurations, including choke, basket, or vertical lifts. Their endless design minimizes wear points and enhances durability.
Applications: Frequently used in scenarios that require regular adjustments to the sling's configuration, such as in construction or assembly lines.
These slings feature reinforced loops (eyes) at both ends, made from either webbing or round materials.
Advantages: The reinforced eyes enhance durability and make it easy to attach to hooks or shackles, providing a secure grip during lifting.
Applications: Commonly employed in construction and manufacturing for lifting beams, machinery, or other large items.
These slings consist of multiple legs made from either webbing or round slings, all connected by a central lifting point.
Applications: Used in construction, shipping, and oil and gas industries for heavy or irregularly shaped loads.
Applications of Textile Slings
Textile slings are frequently employed for lifting prefabricated materials, structural elements, and machinery. Their flexibility allows them to handle irregularly shaped loads without causing any damage.
In manufacturing environments, textile slings are perfect for managing delicate or sensitive equipment, such as glass panels, painted machinery, or polished metals.
Textile slings are commonly used for securing and lifting cargo, whether during the loading and unloading of ships, trucks, or in warehouses.
4. Oil and Gas Industry
In both offshore and onshore operations, textile slings offer corrosion resistance and lightweight handling for pipeline components, drilling equipment, and more.
In projects related to wind and solar energy, textile slings are utilized for the installation of turbines, solar panels, and other sensitive components.
Safety Standards and Regulations
The European Standard EN 1492 pertains to textile slings, including webbing and round slings. This standard ensures that slings are produced, tested, and labeled in accordance with safety and performance criteria. Important aspects include:
- Load Capacity Labeling: Clear markings that show the Working Load Limit (WLL) and safety factors.
- Color Coding: Standardized colors for slings based on WLL to prevent confusion during use.
- Breaking Strength Testing: Slings must undergo thorough testing to confirm their durability and strength
This EU directive addresses the safe design and manufacturing of lifting accessories, including textile slings. It requires:
- CE marking to demonstrate compliance.
- Safety instructions for proper use and maintenance.
- Risk assessments to identify potential hazards during operation.
- Inspection and Certification: Textile slings must be regularly inspected by qualified personnel and certified as safe for use.
- Risk Assessments: Employers are required to perform risk assessments for lifting tasks to ensure the right equipment is utilized.
- Training Requirements: Operators must receive adequate training to safely use textile slings.
- Ensure that lifting equipment, including textile slings, is appropriate for the task at hand.
- Perform regular inspections and testing to uphold safety standards.
- Maintain records of all inspections and certifications.
- Detecting any damage, such as cuts, abrasions, or exposure to chemicals.
- Verifying that labels are clear and intact.
- Replacing any slings that show signs of wear or do not meet safety standards.
- Every textile sling must have traceable information, including the manufacturer's identification, production batch, and manufacturing date.
- Documentation proving compliance with EN 1492 standards is necessary for audits and inspections.
Regulations also promote the proper storage and disposal of textile slings to reduce environmental impact, ensuring that used or damaged slings are recycled in a responsible manner.